Here is a cylinder on the mandrel. The barrel is going to be shortened by .208. Removing the fin on the bottom makes room for the case nuts or any other small obstacles on the case.
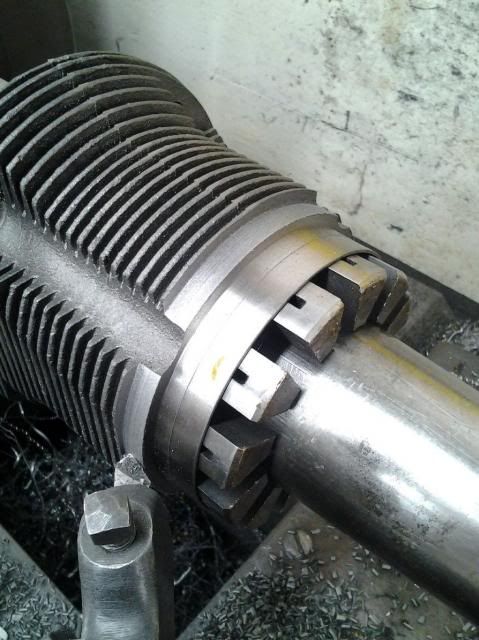
He has two cylinders cut now. This picture shows the .060 head gasket in place and it *just* slips into the hole with zero clearance. He can now establish the pushrod length.

They are 10.975" long after measuring everything. In this picture, the old pushrod is below, the new one is above it. It is now 7/16 on one end, with a straight taper to 3/8 on the small end because of clearance needed at the rocker arm end. Large dimensions like this make an extremely stable valve train. Aluminum is quieter because it dampens shock. This also makes it easier on the valve train and the cam shaft.
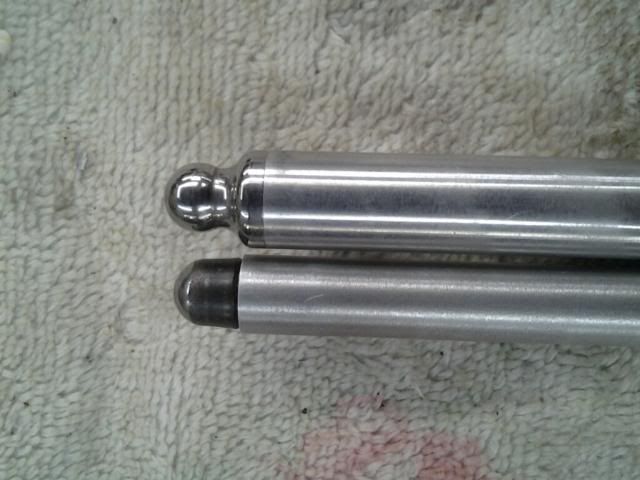
Ray is measuring the cylinders here, checking that they are all exactly the same way after cutting. He had to do a little touch up on a couple of them. Now he will hone them. Within .0001 (average human hair is .0004).
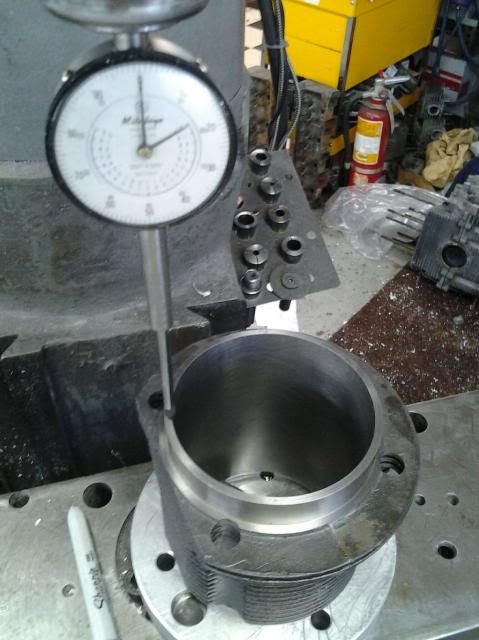
Doing some fitting, it's a bit narrower so he will shorten these studs. After that he will do a valve job on the cylinder heads and start the assembly.
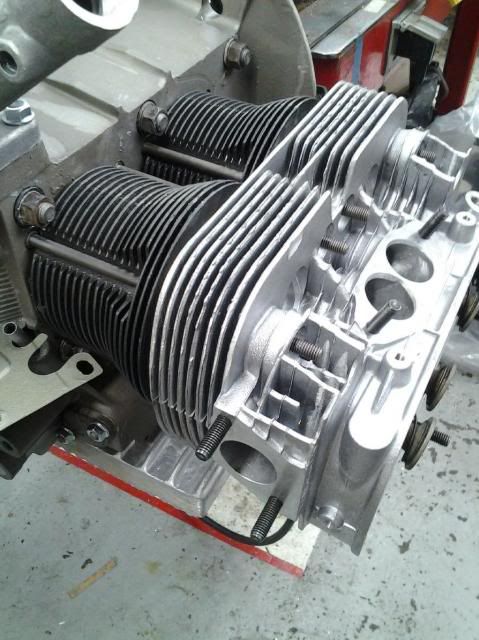
All 16 head studs have been shortened to accommodate the narrower combination.

We are going to have to bead blast the manifolds because these fuel stains will not come off. The clean spot is from modifying the manifold for clearance of the tin, something he always wanted to do but he's never had them off.

After:
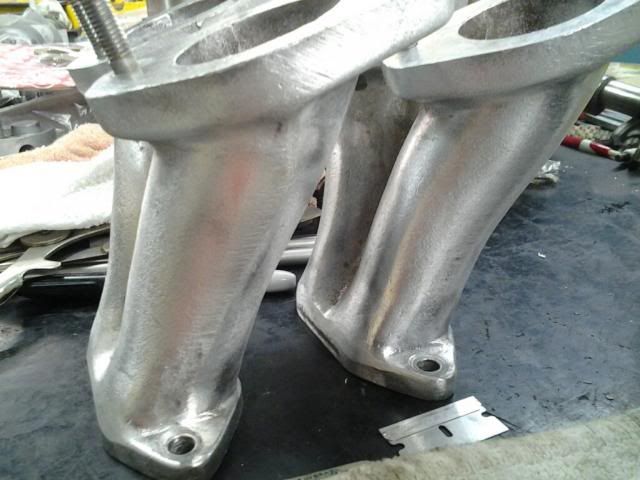
These needs some love. Dual 40 Webers, once dialed in decades ago, we never had to touch them.

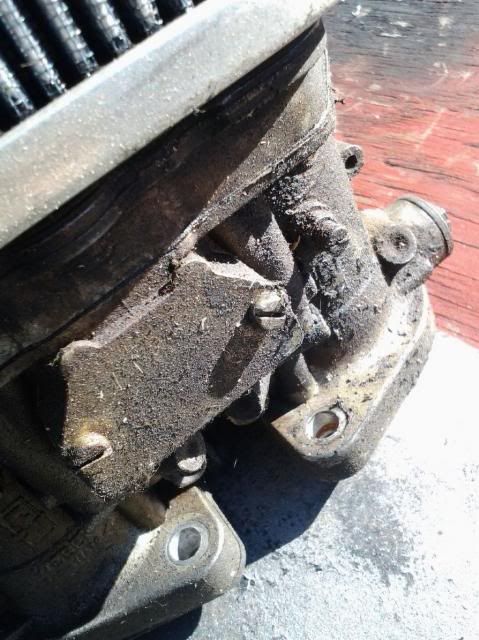