vwhelmot
|
 |
« Reply #60 on: June 18, 2015, 08:51:43 am » |
|
|
|
« Last Edit: June 18, 2015, 09:01:43 am by vwhelmot »
|
Logged
|
|
|
|
vwhelmot
|
 |
« Reply #61 on: June 18, 2015, 09:34:44 am » |
|
|
|
|
Logged
|
|
|
|
|
vwhelmot
|
 |
« Reply #63 on: June 18, 2015, 12:09:24 pm » |
|
Next was to cut a huge hole out. :shock: Updates soon. 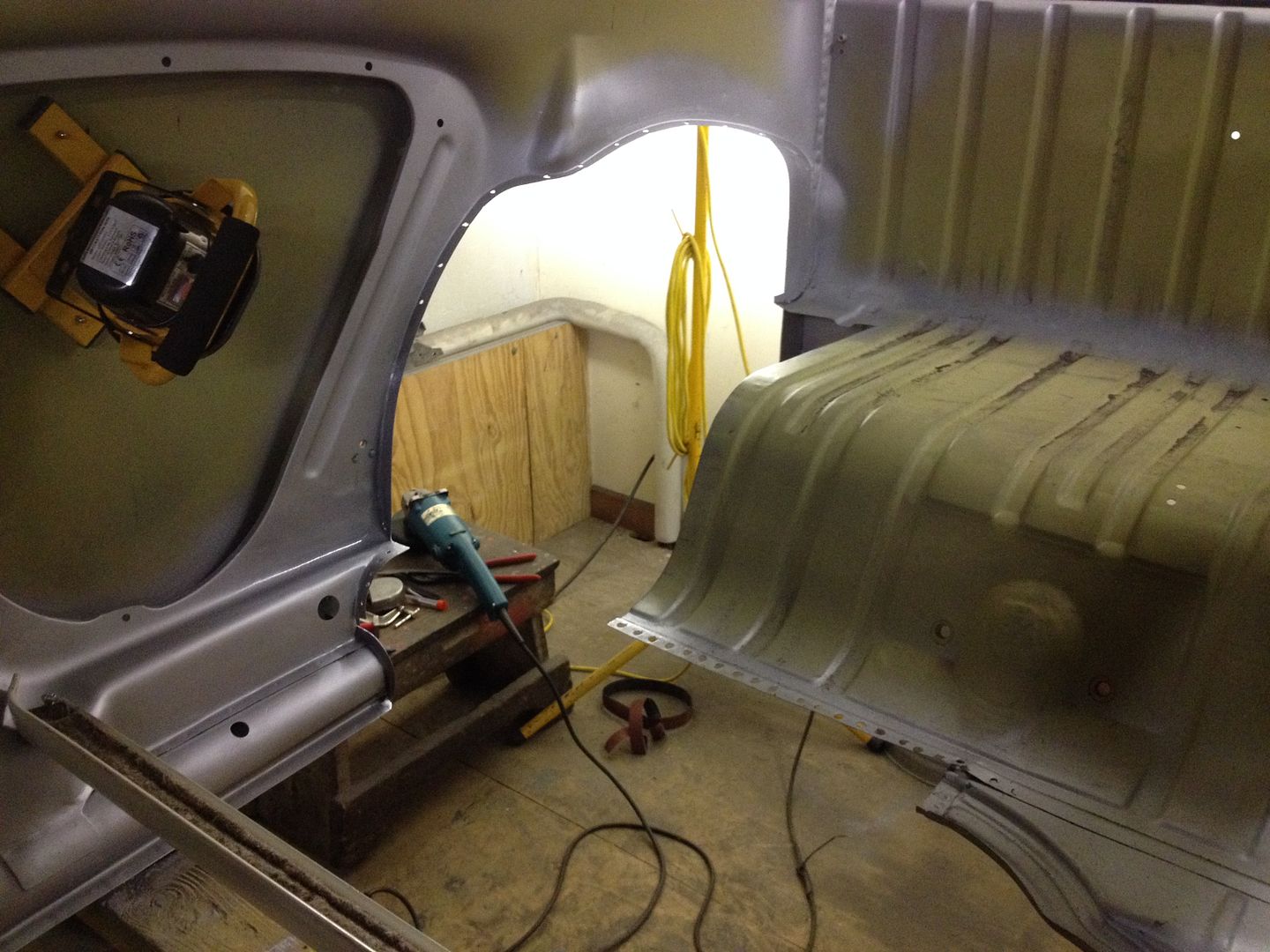
|
|
|
Logged
|
|
|
|
Jeff68
|
 |
« Reply #64 on: June 18, 2015, 13:59:49 pm » |
|
Very nice work to say the least....You're a dedicated hard working VW guy for sure! Keep going! 
|
|
|
Logged
|
|
|
|
vwhelmot
|
 |
« Reply #65 on: June 20, 2015, 12:42:56 pm » |
|
|
|
|
Logged
|
|
|
|
vwhelmot
|
 |
« Reply #66 on: June 21, 2015, 16:47:10 pm » |
|
|
|
|
Logged
|
|
|
|
vwhelmot
|
 |
« Reply #67 on: June 21, 2015, 17:08:10 pm » |
|
|
|
|
Logged
|
|
|
|
vwhelmot
|
 |
« Reply #68 on: June 22, 2015, 09:43:57 am » |
|
|
|
« Last Edit: June 22, 2015, 10:50:57 am by vwhelmot »
|
Logged
|
|
|
|
vwhelmot
|
 |
« Reply #69 on: June 23, 2015, 08:36:43 am » |
|
|
|
|
Logged
|
|
|
|
vwhelmot
|
 |
« Reply #70 on: June 23, 2015, 10:47:08 am » |
|
|
|
|
Logged
|
|
|
|
vwhelmot
|
 |
« Reply #71 on: June 23, 2015, 12:09:20 pm » |
|
|
|
|
Logged
|
|
|
|
vwhelmot
|
 |
« Reply #72 on: June 23, 2015, 12:26:02 pm » |
|
|
|
|
Logged
|
|
|
|
jick
|
 |
« Reply #73 on: June 23, 2015, 12:30:51 pm » |
|
amazing stuff dude!
|
|
|
Logged
|
|
|
|
Neil Davies
|
 |
« Reply #74 on: June 23, 2015, 20:17:19 pm » |
|
Nice work! Be a shame to cover it in carpet...  seriously tho, it shows how far standards have risen in the last 10 years or so. Beetles arent the cheap disposable cars they were. I hope the aftermarket realises that and produces some better repair panels. We've got Hooky and Autocraft, Wolf and Gerson for the early stuff, but I'd like to see companies like Veng and Klokkerholm just looking after their tools to produce decent quality panels in reasonable thickness steel. Anyway, rant over! Please continue with putting my repairs to shame! 
|
|
|
Logged
|
2007cc, 48IDFs, street car. 14.45@93 on pump fuel, treads, muffler and fanbelt. October 2017!
|
|
|
vwhelmot
|
 |
« Reply #75 on: June 23, 2015, 20:49:41 pm » |
|
I totally agree mate. I've found since starting the rebuild that there is a lack of decent repair panels for sixties bugs. There seems to be more available for earlier cars, even splits. I suppose it's a demand thing, maybe now as people are repairing sixties bugs to a nice standard the panel companies may take note and start offering correct pressings that not only fit but look right too. Easier said than done I suppose. I'm glad companies like hookys and virtanen , wolf and autocraft are about. I've tried to tell Steve Hook to look into cross members and boot floor edges as these are common rust areas. PS, no carpet is covering my repairs , not even the front. 
|
|
|
Logged
|
|
|
|
vwhelmot
|
 |
« Reply #76 on: June 24, 2015, 11:25:54 am » |
|
|
|
|
Logged
|
|
|
|
|
vwhelmot
|
 |
« Reply #78 on: June 24, 2015, 13:29:29 pm » |
|
|
|
|
Logged
|
|
|
|
vwhelmot
|
 |
« Reply #79 on: June 25, 2015, 14:29:27 pm » |
|
|
|
|
Logged
|
|
|
|
vwhelmot
|
 |
« Reply #80 on: June 26, 2015, 14:56:12 pm » |
|
|
|
|
Logged
|
|
|
|
vwhelmot
|
 |
« Reply #81 on: June 26, 2015, 15:03:18 pm » |
|
|
|
|
Logged
|
|
|
|
vwhelmot
|
 |
« Reply #82 on: June 26, 2015, 15:12:06 pm » |
|
|
|
|
Logged
|
|
|
|
karl h
|
 |
« Reply #83 on: June 26, 2015, 17:50:47 pm » |
|
so you are trying to impress us, huh? you know what - it works!  i did most of these areas a couple of times and it didnt remotley look as clean - stellar work, bud
|
|
|
Logged
|
|
|
|
Iryanu
|
 |
« Reply #84 on: June 26, 2015, 23:40:53 pm » |
|
This thread is off the hook.  Kudos.
|
|
|
Logged
|
|
|
|
vwhelmot
|
 |
« Reply #85 on: June 27, 2015, 08:43:10 am » |
|
|
|
|
Logged
|
|
|
|
vwhelmot
|
 |
« Reply #86 on: June 27, 2015, 09:26:06 am » |
|
|
|
|
Logged
|
|
|
|
|
vwhelmot
|
 |
« Reply #88 on: June 27, 2015, 09:39:07 am » |
|
|
|
|
Logged
|
|
|
|
vwhelmot
|
 |
« Reply #89 on: June 29, 2015, 21:18:17 pm » |
|
|
|
|
Logged
|
|
|
|
|